[뉴스비전e 이진구 기자] 증착기술은 디스플레이에 있어 핵심 기술이다.
LDC에 이어 OLED 산업의 상용화는 물론, 태양광 박막형 태양전지의 효율성에 있어 증착 과정의 간결성과 정확성은 전체 산업의 성패를 가름할 정도의 중요성을 지닌다.
최근 한상범 LG디스플레이 부회장은 CES 2018 기간 동안 "OLED 사업전환을 가속하고, 이와 관련한 매출을 전체의 40%까지 끌어올리겠다"고 발표했다.
삼성디스플레이와의 격차를 크게 벌려 대형 OLED 분야에서 입지를 확실히 다지겠다는 의미로, 이 목표를 좌우할 핵심 키 중 하나는 증착기술이다.
◆태양전지 효율성을 결정하는 증착기술
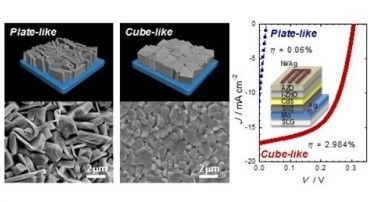
한국은 과거 2008년 이명박 정부의 핵심정책인 녹색에너지 정책을 통해 태양광산업 발전을 촉진해 왔다. 정권이 바뀌긴 했어도 친환경 에너지에 대한 중요성은 계속 강조되고 있지만, 보급 속도가 더딘 이유 중 하나라 증착기술의 한계로 인한 효율성이 제자리에 있기 때문이다.
폴리실리콘을 이용한 태양전지는 가격 상승과 변동폭의 이유로 경제적 타산이 맞지 않았고, 유리 및 금속을 활용한 박박 전지는 효율성, 이른바 '광변환효율'이 낮았다.
이달초 논문으로 게재된 전남대학교 연구팀이 주석 황화물 기반 박막태양전지의 가격경쟁력을 높이는 연구결과의 핵심은 증착기술이다.
전남대 연구팀은 기상증착법을 활용, 주석 황화물의 형상제어 기술을 확보했다. 이를 통해 기존 판상 형태의 표면이 아닌, 고밀도의 정육면체 형태의 표면(모폴로지)를 형상할수 있게 됐고, 이 기술은 대면적 소자 제작에 활용도가 높다는 결론을 내렸다.
결론적으로, 증착기술 효율화를 통해 장기간 공기노출 상태에서도 태양전지의 효율을 9.85%를 유지할수 있도록 했고, 상용화를 할 경우 기존 카드큠 황화물 기반 박막태양전지 중 가장 높은 효율을 달성할수 있게 됐다.
◆고해상도 OLED 구현의 핵심으로 부각된 증착 공정
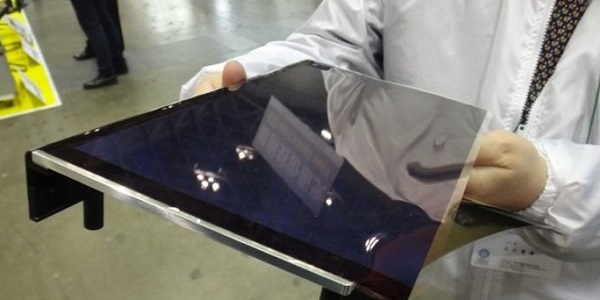
TV시장이 고해상도를 쫒아 재편되면서, 디스플레이 산업에 있어서도, 증착기술의 중요성은 더욱 부각되는 양상이다.
UHD 해상도를 채택한 제품이 표준화되면서 UHD(4K) 콘텐츠도 본격적으로 상용화되는데 이어, 올해 평창올림픽과 2020년 도쿄올림픽을 목표로 8K 콘텐츠가 제작될 예정이다. TV용 디스플레이도 8K 이상의 제품들이 쏟아져 나올 태세며, 지난해 초부터 모바일용 디스플레이 시장에서는 UHD 해상도의 LCD를 적용한 스마트폰이 출시되기도 했다.
OLED도 QHD 해상도로 빠르게 변화해가고 있다.
중소형 OLED 제품에서 고해상도의 OLED를 제조하는 데에 있어 가장 먼저 부딪히 3원색인 RGB 픽셀을 만드는 핵심인 증착 공정(Deposition)이다.
증착 공정은 챔버(Chamber) 하단에 위치한 증착 소스에서 유기물을 가열하며, 이로써 가열된 유기물은 승화된다.
승화된 유기물은 상부에 위치한 FMM(Fine Metal Mask)을 통과해, TFT(Thin Film Transistor)에 증착된다. 메탈마스크에는 일정한 패터닝이 되어 있는 부분에만 유기물이 입혀지는 것 이른바 증착이 되도록 하는 안내가 돼 있다. 이를 패터닝이라고 한다. 그러니까 FMM은 이런 패터닝 처리가 돼 있는 메탈마스크로, 이 두께가 얇을수록 고해상도를 구현할수 있다.
문제는 고해상도를 위해 FMM의 두께가 15마이크로미터(1000분의 15 밀리미터) 이하로 얇게 되야 하는데, 얇아질수록 제조공정이 난해해 지는 것이다. 이에 따라 제조과정의 불량이 발생하고, 결국 수율(정상 제품으로 만들어내는 비율)이 내려가 상업성이 떨어진다는 것이다.
증착장비 업체 관계자는 "패터닝 단계에서의 배치가 상당 수준으로 일정해야 하는 정밀도도 해결해야 할 과제로 남아있다"며 "고해상도를 구현하기 위해 디스플레이 장비업체들은 물론 주요 연구기관들도 여러 가지 방법으로 효율적인 방식을 개발중인데, 결국 상용화에 있어 채택되는게 관건"이라고 설명했다.
◆고해상도를 구현하기 위한 대안들은?
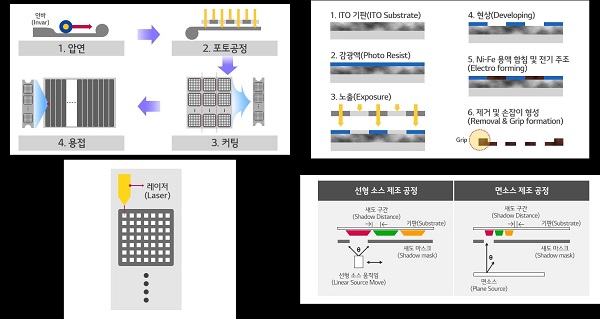
이를 해결하기 위한 방안들로, ▲전기주조방식, ▲레이저 패터닝 방식 ▲면형 제조방식 등 다양한 연구가 진행중이다.
먼저 ▲전기 주조방식은 ITO(Indium-Tin Oxide; 인주석 산화물) 기판에 원하는 모양을 잡아 감광액(Photo Resist; PR)으로 패터닝 한 이후, 니컬과 철(Ni-Fe)의 합성 용액에 넣고, 원하는 두께만큼 금속을 쌓아 올리는 방식이다. 이와 같은 방식으로 감광액을 제거함으로써 FMM을 제조하는 방식이다.
두번째 ▲레이저 패터닝(Laser Patterning은 금속판에 레이저를 조사하는 방식으로, 아주 미세한 움직임까지도 반영하여 형태화할 수 있다는 장점이 있다. 이어 ▲면형 제조방식 이른바 '면소스(Plane Source)' 기술은 현재 양산되고 있는 선형 소스를 면소스로 바꾸는 방식이다. 이를 통해 유기재료의 입사각이 감소할 수 있어, 기존 FMM을 사용하면서도 색감이 튀는 현상을 줄일 수 있다.
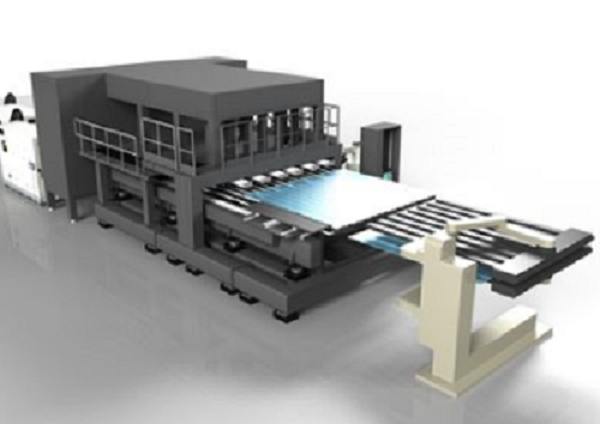
일본의 디스플레이 장비업체인 브이테크(V-tech)는 이와 같은 파인메탈마스크 기반에서의 고해상도 구현을 증착공정상의 대안을 아예 뛰어 넘어, 하이브리드형 메탈마스크를 개발하는 등 OLED 기술 완성도를 위해 주요국 기업들이 도전중이다.